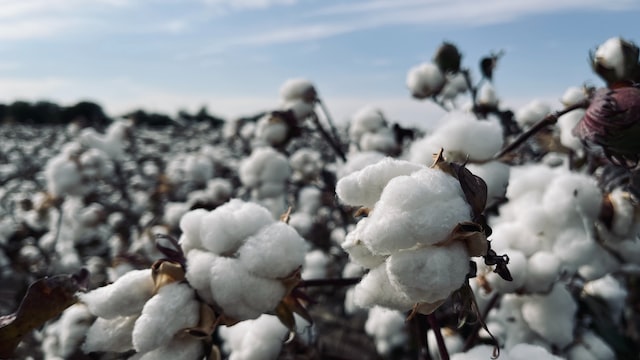
Overview
Cotton dust is often present in the air during cotton handling and processing. Cotton dust may contain many substances including ground plant matter, fibre, bacteria, fungi, soil, pesticides, non-cotton matter, and other contaminants. These may have accumulated during growing, harvesting, and subsequent processing or storage periods. Let’s dive into occupational exposure to cotton dust and the dangers of such exposure.
Health effects of cotton dust
Byssinosis, also called brown lung or brown lung disease, is a respiratory disorder caused by inhalation of an endotoxin produced by bacteria in the fibres of cotton. Byssinosis is common among textile workers, who often inhale significant amounts of cotton dust. Cotton dust may stimulate inflammation that damages the normal structure of the lung and causes the release of histamine, which constricts the air passages. As a result, breathing becomes difficult. Over time the dust accumulates in the lung, producing a typical discolouration that gives the disease its common name.
Exposure to cotton dust
Employees may potentially be exposed to cotton dust during cotton handling, harvesting, processing as well as during storage. For the wool industries, typically dusty operations include opening, blending, carding, and backwinding. Furthermore, early processes including raw material handling, opening, carding, drawing, combing, beaming, ring spinning, and high-speed winding are likely to generate cotton dust resulting in employee exposure.
Controls of cotton dust
It isn’t possible to eliminate process dusts from mills, but it may be possible to reduce the quantity of dust produced. Batches of cotton and wool vary in their dustiness, depending on the quality of the raw material, the treatment it receives and the processes through which it is put. Consideration should be given on reduction of dust as one of the objectives when introducing new processes or machines or when changing existing ones.
The most effective approach is to enclose machinery as much as possible and then to use Local Exhaust Ventilation to control dust escaping from essential openings. Good general ventilation is also necessary to prevent the build-up of high background dust levels. Exposures can also be reduced by removing workers from close contact with the process, for example by eliminating the need to enter blending bins or by placing workers in booths fed with filtered air where this is feasible.
Cleaning should be done using a vacuum cleaner, not a broom or brush or compressed air. Cleaning machinery by ‘flapping down’ with cardboard, using brooms, brushes or using compressed air is strongly discouraged. High levels of dust can be generated by disturbing settled dust. A vacuum cleaner with a type H cleaner suitable for industrial use should be used. Or a vacuum cleaner fitted with a HEPA filter. If brushing floors cannot be avoided, then dust generation can be reduced by first moistening the floor with water.
Emptying dust collectors is a very dusty task and RPE should be worn if dust cannot be adequately controlled during emptying. Filter systems should be regularly emptied and well maintained in good working condition. This reduces dust generation when emptying dust collectors.
Occupational cotton dust management plan
Apex Environmental is SANAS 17020 accredited. We are a Department of Labour Approved Inspection Authority (AIA), offering specialist Environmental and Occupational Hygiene monitoring services. Apex Environmental specialises in Occupational Hygiene, Environmental Monitoring and Risk Assessments, Training and Monitoring Equipment Sales. We recognise the benefits of strong partnerships, accurate data, comprehensive reports and superior service. Contact Apex Environmental to arrange occupational monitoring in your workplace.