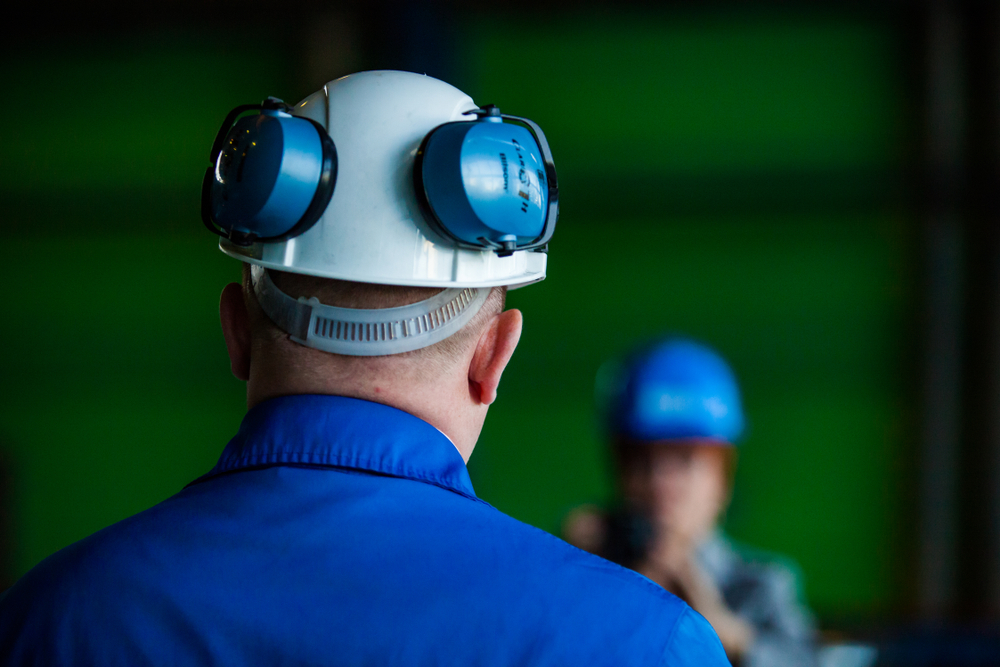
Controlling the Risks from Vibration
When it comes to workplace hazards and risks, vibration is often overlooked due to its seemingly innocuous effect on our bodies. However, as with all workplace risks, it is a concern when employees are exposed to it for prolonged periods of time and in cases where there may be severe jolting. To better understand how to control this risk, we’ll first take a look at what the risks from vibration present.
Back pain and vibration
Sitting for extended periods of time, such as what is required of drivers or heavy machinery operators, often brings about back pain. In some cases, this is the driver’s fault, from poor posture to making incorrect adjustments that have left them in an uncomfortable position. There are also some cases where equipment controls are the issue, such as needing to twist or stretch oneself in order to see properly. All of these factors are likely to cause back pain, which is then amplified by the whole-body vibration that the equipment generates and can cause serious harm.
Hand-arm vibration
Another risk that vibration presents is hand-arm vibration syndrome (HAVS). The long-term effects of HAVS are loss of fine motor skills, pain, distress, loss of sleep, reduced grip strength and finger blanching attacks triggered by cold or wet environments. HAVS can also onset other diseases, such as carpal tunnel syndrome.
Hand-arm vibration is often observed in handheld machinery which emit vibration, including hand-held power tools, such as road breakers, and hand-guided equipment, such as powered lawnmowers, or by holding materials being processed by machines, such as pedestal grinders.
Is everyone at risk?
Thankfully, not everyone is at risk of injury through vibration. Firstly, risk is calculated based on severity in relation to duration of exposure – meaning that exposure to vibration within a certain range wouldn’t be considered harmful, particularly within the regular duration of shift work.
Secondly, the cases in which employees are exposed to hazardous levels of vibration are limited. An example of this would be that a road transport vehicle driver would be at a far lesser risk of whole-body vibration in comparison to an off-road driver due to the fact that the shock absorbers of the road vehicle would absorb the majority of the vibration.
It is important to bear in mind that elderly employees and those with previous injuries are at risk to vibration-related injuries and should take extra precautions to ensure they are able to perform their work safely. For young staff and pregnant women, it is best to avoid the risk altogether.
Exposure Action Value and Exposure Limit Value
These are two important terms to familiarise yourself with as they speak to health and safety legislation which workplaces must abide by.
Both values are plotted out on graphs with vibration magnitude, measured in meters squared, on one axis and duration of exposure, measured in hours, on the other.
Exposure action value plots the curve of exposure to show the point where action should be taken. As already mentioned, small amounts of vibration need not necessarily be harmful, so anything below the exposure action value need not warrant preventative action.
Exposure limit value plots the curve of exposure to show when the vibration exposure is deemed to be too hazardous and steps should be taken to lower the exposure, thus bringing the risk back into a manageable range.
What can employers do to manage the risks from vibration?
As with all workplace risks, employers are required to do what they can to ensure their employees’ safety. This starts with an assessment to plot where they sit on the graph mentioned above. This is best done by an expert, such as the vibration assessments that Apex Environmental offers. With this information, employers can take the necessary steps to better manage the risk that their employees are exposed to.
Should the risk be too great, an employer could consider:
- Alternative work methods: There may be workarounds available that allow you to negate the risk of vibration by eliminating the need for exposure in the first place. Employers may want to reconsider their workflow as a whole to avoid the use of machinery that pose a vibration risk. Alternatively, an employer may want to invest into automating the process.
- Equipment selection: Similar to the above, an employer may reconsider which equipment gets used in order to limit vibration exposure. Power tools often help get the job done faster, but there are often alternatives available which do not expose its user to vibration.
- Utilising a policy to replace old equipment: It’s normal to replace equipment as it wears, so it is important to bear vibration risk in mind when making purchase decisions. Staff may need to be trained on this new equipment, however, particularly if it has additional features to limit vibration exposure.
- Maintenance: A good maintenance programme can ensure equipment and machinery are in good working condition, eliminating avoidable increases in vibration levels due to misalignment, detuning or bluntness.
- Work schedules: Since the duration of exposure is a key part of the equation, an employer may want to consider shortening shifts so as to decrease the amount of time employees are exposed to high levels of vibration.
- Protective gear: There isn’t much protective gear that can assist with vibration, but clothing and gloves may help make a difference.