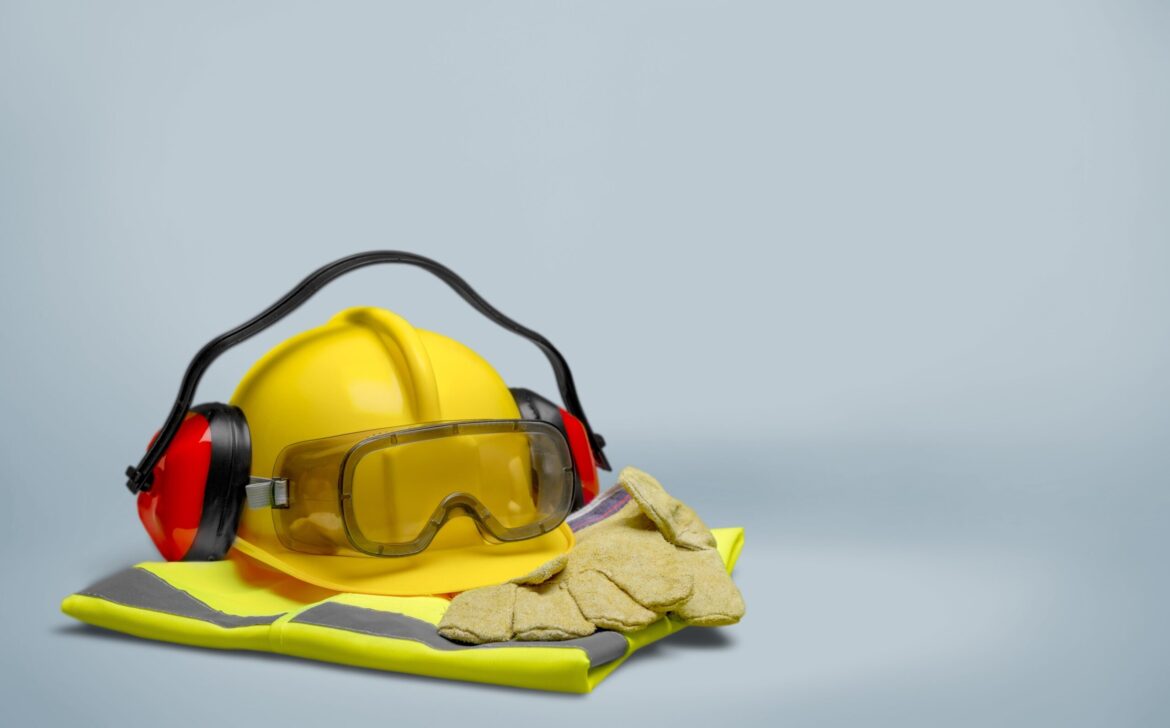
The Importance of PPE in Ensuring Worker Safety: A Comprehensive Guide
Personal Protective Equipment (PPE) plays a crucial role in maintaining worker safety across various industries. Whether in construction, healthcare, manufacturing, or chemical handling, PPE is essential to minimize risks associated with workplace hazards. This comprehensive guide explores the significance of PPE, its types, regulatory standards, and best practices for implementation.
Understanding Personal Protective Equipment and Its Purpose
PPE refers to specialized clothing or equipment worn by workers to protect against workplace hazards. These hazards can include physical injuries, chemical exposure, biological contaminants, radiation, and extreme environmental conditions. The primary purpose of PPE is to serve as a barrier between the worker and potential dangers and increase worker safety thereby reducing the likelihood of injuries and occupational illnesses.
Types of PPE
Different types of PPE are designed to address specific workplace hazards. The most common categories include:
Head Protection
- Helmets and hard hats protect workers from falling objects, electrical shocks, and impact injuries.
- Common in construction, mining, and industrial settings.
Eye and Face Protection
- Safety glasses, goggles, and face shields protect against debris, chemical splashes, and harmful radiation.
- Essential in laboratories, welding, and healthcare settings.
Hearing Protection
- Earplugs and earmuffs help prevent hearing loss due to prolonged exposure to high noise levels.
- Used in industries such as aviation, manufacturing, and construction.
Respiratory Protection
- Masks and respirators filter airborne contaminants, including dust, fumes, and pathogens.
- Critical for healthcare workers, painters, and chemical industry employees.
Hand and Arm Protection
- Gloves made of different materials (e.g., latex, nitrile, leather) protect against cuts, burns, and chemical exposure.
- Used in laboratories, food processing, and heavy machinery operations.
Body Protection
- Coveralls, aprons, and high-visibility clothing shield workers from heat, chemicals, and visibility hazards.
- Essential in hazardous material handling and outdoor work environments.
Foot Protection
- Safety boots with steel toes, slip-resistant soles, and puncture protection safeguard against falling objects and chemical spills.
- Common in construction, warehouses, and manufacturing.
PPE and Occupational Hygiene
Occupational hygiene is a field dedicated to identifying and controlling workplace hazards to protect workers’ health. PPE plays a significant role in occupational hygiene by serving as a last line of defence when other control measures, such as engineering or administrative controls, are insufficient. Properly selected and used PPE helps prevent exposure to harmful substances and physical dangers, contributing to a healthier work environment.
The integration of PPE with occupational hygiene strategies ensures that workers are protected from both immediate and long-term health risks. For instance, respiratory protection is essential in environments with airborne contaminants, while gloves and protective clothing help reduce exposure to hazardous chemicals. By combining PPE with regular workplace assessments and hazard control measures, employers can create safer working conditions.
A key aspect of occupational hygiene is the proper training and awareness of PPE use. Workers must understand when and how to use PPE effectively, as well as the limitations of their protective equipment. Employers should conduct regular training sessions and refresher courses to ensure compliance and reinforce safe practices. This proactive approach reduces workplace illnesses and injuries while fostering a culture of worker safety.
Additionally, ongoing evaluation of PPE effectiveness is crucial for occupational hygiene programs. Employers should regularly assess whether the provided PPE meets industry standards and remains suitable for the tasks at hand. Workers should be encouraged to report any issues related to PPE fit, comfort, or performance. By continuously monitoring and improving PPE use, organizations can enhance worker protection and uphold high occupational hygiene standards.
Regulatory Standards for PPE
Governments and occupational safety organizations have established standards for PPE usage to ensure workplace safety. Some key regulatory bodies include:
- Occupational Safety and Health Administration (OSHA) (USA)
- European Agency for Safety and Health at Work (EU-OSHA)
- National Institute for Occupational Safety and Health (NIOSH)
- International Organization for Standardization (ISO)
Employers must comply with these regulations to protect workers and avoid legal consequences. Compliance includes providing appropriate PPE, ensuring proper fit and maintenance, and offering training on its correct usage.
The Role of Employers and Employees in PPE Implementation
Employer Responsibilities
- Conduct hazard assessments to identify risks requiring PPE.
- Provide appropriate and well-fitted PPE at no cost to workers.
- Train employees on PPE usage, maintenance, and disposal.
- Regularly inspect and replace worn-out or damaged PPE.
Employee Responsibilities
- Wear PPE correctly and consistently while performing tasks.
- Report any defective or ill-fitting PPE to supervisors.
- Follow workplace safety protocols and attend PPE training sessions.
Challenges and Solutions in PPE Implementation
Despite its importance, PPE usage faces challenges such as:
- Lack of awareness or training: Workers may not fully understand the risks or proper usage of PPE.
- Comfort and fit issues: Ill-fitting PPE can lead to discomfort and reduced compliance.
- Neglect and non-compliance: Some workers may ignore PPE requirements due to inconvenience.
Solutions:
- Conduct regular safety training sessions.
- Provide PPE options that balance comfort and protection.
- Enforce strict PPE policies with disciplinary measures for non-compliance.
PPE and Workplace Safety
PPE is a fundamental aspect of workplace safety, protecting workers from various hazards that could lead to severe injuries or illnesses. Proper implementation, compliance with safety standards, and fostering a culture of safety can significantly reduce workplace accidents. Employers and employees must work together to ensure PPE is used effectively, creating a safer and healthier work environment for all