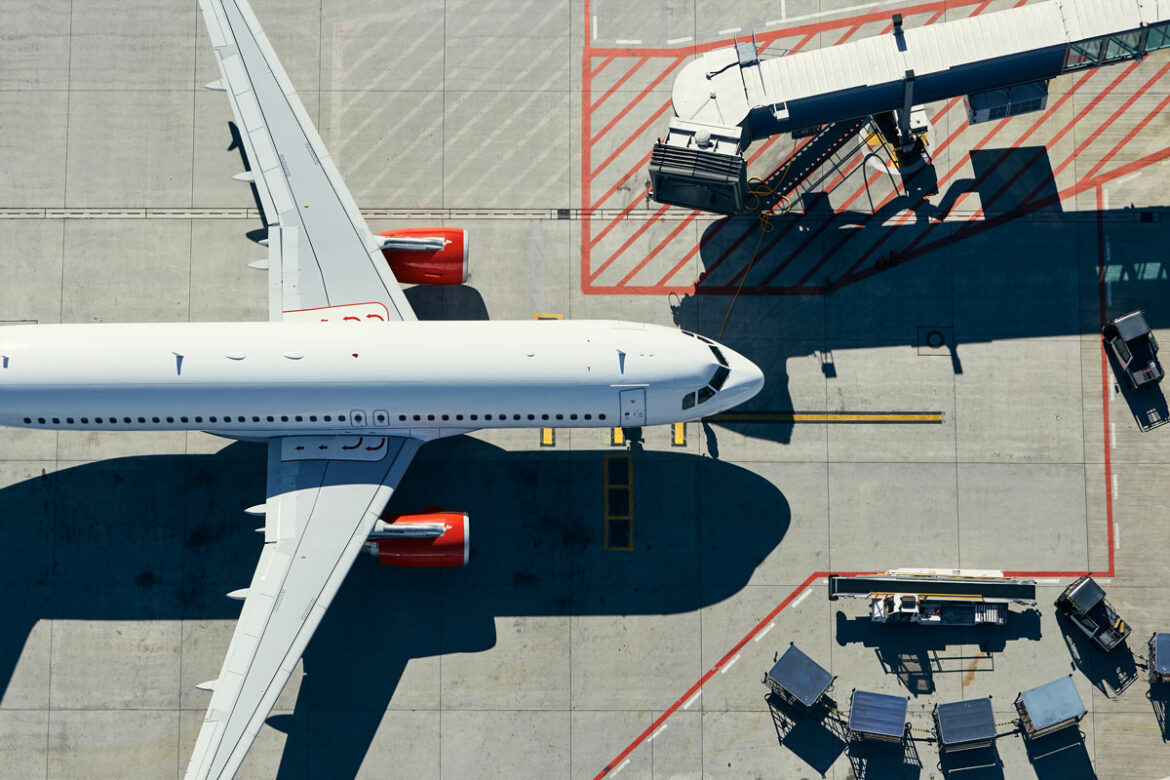
An overview of airside occupational health and safety hazards
Globally, the aviation sector provides approximately 87.7 million jobs. It creates employment opportunities within the various sub sectors of the industry such as the numerous service providers at airports, airline staff and organization providers. The aviation industry is essential to the daily functioning of the global economy. It connects people from one part of the world to another. Additionally, it is a pivotal component of the global logistics sector for the trade of goods, together these industries generate $2.7 trillion annually, which amounts to 3.6% of the world’s GDP.
However, the exponentially growing strain on airports around the world has led to the need for faster flight turnaround times. This increased demand, coupled with other pressures such as high employee turnover leads to staff that are less trained which in turn contributes to the enormous number of injuries in the aviation industry. This article will provide an overview of the various occupational hazards faced by employees in the aviation industry, control measures in place and areas in which they can improve.
Occupational hazards
Baggage handling: manual lifting and moving of luggage can cause serious injuries that may arise from the lifting of baggage; that is overweight, in a repeated motion, in strenuous positions for loading and offloading the aircraft. Furthermore, these workers are exposed to machines with conveyor belts that can cause entrapment and crushing injuries.
Working at heights: numerous jobs involving aircrafts require employees to work at heights. Injuries that involve falling from heights usually occur; during aircraft maintenance, when getting in and out of the aircraft, when loading and offloading the aircraft.
Moving vehicles: there are always a large volume of vehicles moving around in an airport, whether it be for refuelling, taxing, towing, maintenance, or mobile aircraft steps. Injuries can occur due to not being able to hear the vehicle approaching because of the background aircraft noise, and the use of hearing protective equipment.
Noise: it is common knowledge that aircrafts make alot of noise; on average it is about 35db above the occupational exposure limit for noise. With just over three hundred landings daily prolonged exposure can cause significant and irreparable harm to employees.
Extreme temperatures: these conditions put workers at risk of heat stroke, being hit by foreign object debris in windy conditions and frostbite in wintry conditions.
Foreign object debris: any object found in an inappropriate area that can cause injury to employees or equipment through jet blast or heavy winds.
Chemical hazards/fuel emissions: prolonged exposure to tiny amounts of carbon monoxide and diesel and jet exhaust fumes can cause headaches, impaired judgment fatigue, cancer and can even be fatal depending on the level of exposure.
Biological pathogens: millions of travellers pass through airports every year, and the risk of being exposed to pathogenic substances increases. Exposure to these pathogens come from blood, saliva, waste, and infectious organisms that cause covid-19, bola, and yellow fever.
Occupational stress: airport ground staff must often juggle between strenuous workloads, working long hours on shift coupled with insufficient break times and other occupational related hazards.
Control measures
Baggage handling:
Provide regular information and training on the correct lifting and handling methods, as well as how to guides on the use equipment in a safe manner.
Invest in automation equipment to assist baggage handlers with the loading and offloading the aircraft to avoid ergonomic strain.
Working at heights:
Ensure that equipment used is stable and well suited for its purpose.
Ensure equipment used is maintained regularly and can prevent injuries, slips and falls.
Information and training must be provided for staff who are required to work at heights.
Noise:
High quality hearing protection must be provided must be provided to employees
Noise zones must be clearly demarcated, and no person shall be permitted into this area without the correct HPE.
Noise-risk assessments must be regularly conducted to ensure that control measures are still effective.
Moving vehicles:
Employees must stick to designated walking areas and must always be vigilant of their surroundings.
High visibility PPE must always be worn to reduce the risk of being hit by moving vehicles.
Extreme temperatures:
Provide regular information and training on the risks associated with different thermal extremes and how to prevent them, e.g., consistently hydrating in very hot conditions.
Ensure that the correct PPE is worn for the different thermal environments.
Allow for adequate breaks for employees and that ensure administrative measures such as rotation and limiting exposure are used.
Foreign object debris:
Ensure employees are regularly trained and given information to ensure the prevention of FOD related injuries and on the correct use of PPE
Maintenance and inspection systems must be put in place to ensure that FOD is appropriately identified and removed.
Chemical hazards/fuel emissions: fuel emissions:
Establish a medical surveillance programme for individuals working at high-risk areas to prevent, monitor and detect early signs of respiratory and other health issues related to fuel emission exposure.
Provide training programs to educate airport staff about the health risks associated with fuel emissions exposure and the importance of following safety protocols
Biological pathogens:
Implement measures such as controlled access points, screening procedures, and regular inspections to minimize the risk of contamination.
Provide appropriate personal protective equipment (PPE) for airport personnel who may be at risk of exposure to hazardous biological agents.
Raise awareness about symptoms, transmission pathways, and proper reporting procedures for suspected cases of biological agent exposure.
Conduct regular inspections of ventilation systems, air quality, and surfaces to identify and address potential sources of contamination.
Implement realistic workload expectations and consider flexible scheduling options when possible.
Occupational stress:
Provide comprehensive training to enhance employees’ skills and confidence and ensure that staff are adequately prepared for their roles.
Provide employees with a degree of control over their work tasks. In addition, allow for decision-making within their scope of responsibility.
Train supervisors and managers to recognize signs of stress and offer support.
Conduct workshops on stress management and coping strategies. Furthermore, educate employees on recognizing signs of stress in themselves and their colleagues.
Conclusion
Airport employees are faced with a plethora of workplace hazards, most of which can’t be eliminated or avoided as it comes as a collective in this field of work. Therefore, it is imperative for employers to ensure that comprehensive risk assessments are carried out, and appropriate yet reasonable control measures are implemented. In addition, regular information, and training as well as PPE must be provided to all staff relative to their job descriptions and interactions. Whilst the aviation industry has excellent safety procedures, more must be done to ensure their implementation and continuous improvement for a safer workplace environment.
https://atag.org/industry-topics/supporting-economic-social-development
https://veriforce.com/blog/airport-construction-hazards-10-risks-you-must-know
https://www.astutis.com/astutis-hub/blog/airport-health-and-safety
https://www.icao.int/sustainability/Documents/AVIATION-BENEFITS-2019-web.pdf
https://www.mcrsafety.com/blog/airline-industry